|
· www.tappi.org
· Subscribe
to Ahead of the Curve
· Newsletters
· Ahead
of the Curve archived issues
· Contact
the Editor

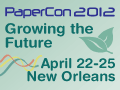
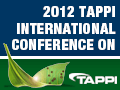
|
|
|
|
Supply Chain Risk Lessons from Post-tsunami Japan
by Kelly Marchese, Siva Paramasivam and Michael Held
Despite the widespread impact of Japan's tsunami on global supply chains, most companies are not fundamentally changing how they manage supply chain risk. Meanwhile, supply chain risks appear to be rising, driven by a variety of internal and external forces. High impact, low probability "black swan" events now seem to be almost a regular occurrence. This is happening more often because in a globally interconnected business environment, problems that used to remain isolated now have far-reaching effects.
A MORE HOLISTIC VIEW OF SUPPLY CHAIN RISK
In today's hyper-connected supply chain environment, risks are evolving at a dizzying pace and can strike from almost any direction. There is a need for a more holistic view of supply chain risk, which should include four distinct risk categories:
- Macro environment risks are broad external forces that affect
the entire business and supply chain. For example, globalization can
give businesses access to less expensive labor and materials, and
opens up vast new markets. It also increases supply chain complexity,
increases the probability and magnifies the impact of disruptions
that in the past might have remained locally isolated.
- Extended value chain risks center around a company's upstream
and downstream supply chain partners. Increased use of outsourcing,
for example, may have improved efficiency and has allowed businesses
to focus more attention on their core competencies. But it has also
made their operations more complex and exposed them to increased third-party
risk.
- Operational risks are tied to a company's internal manufacturing
and distribution operations. Lean manufacturing, just-in-time inventory,
and capacity rationalization may have boosted supply chain efficiency
and may have made businesses more agile and responsive. But by reducing
slack in the network, they have also reduced the margin for error
and amplified the potential for disruptive problems.
- Functional risks relate to the business functions that support
supply chain activities, such as finance, HR, legal, and IT. Many
of today's supply chains are enabled and accelerated by a broad suite
of applications and systems. A disruption or breach in these critical
systems can have an immediate impact on the customer experience.
THE FOUR PILLARS OF A RESILIENT SUPPLY CHAIN
Given the scale and scope of today's global supply chains, there is no way for a company to predict and prepare for every possible risk. However, what a company can do is build resilience. A business with a resilient supply chain can sidestep a wide range of risks and be able to bounce back quickly from risks that cannot be avoided.
Resilience is a characteristic many enterprises and supply chains have long aspired to. To make it happen, organizations should understand the essential components that are required to build resilience. These four capabilities are key:
- Visibility -- being able to track and monitor supply chain events and patterns as they happen or before they happen.
- Flexibility -- being able to promptly adapt to problems without significantly increasing operational costs.
- Collaboration - being able to work effectively with supply chain partners in order to avoid disruptions and achieve common goals.
- Control -- having clearly defined policies, monitoring, and control mechanisms to help ensure that proper procedures and processes are actually followed.
LOOKING AHEAD
In a world where local problems in one region can bring an entire global supply chain to its knees, a business-as-usual approach to supply chain risk is just asking for trouble.
Companies that were fortunate enough to not be deeply affected by last year's disaster cannot afford to sit idle. They should use the experiences of others as a catalyst for building resilience into their own supply chains. Those that don't could end up learning things the hard way when the next disaster strikes.
Kelly Marchese is a Principal, Siva Paramasivam is a Senior Manager
and Michael Held is a Specialist Leader, all in the Supply Chain and
Manufacturing Operations practice in Deloitte Consulting LLP. An expanded
version of this article originally appeared in IndustryWeek magazine.
Now that you
are Ahead of the Curve, stay there by joining TAPPI. For a modest
investment of $174, receive more than US$ 1000 in benefits in return.
Visit www.tappi.org/join
for more details. |
|