An early glimpse at APP’s OKI Mill, Sumatra
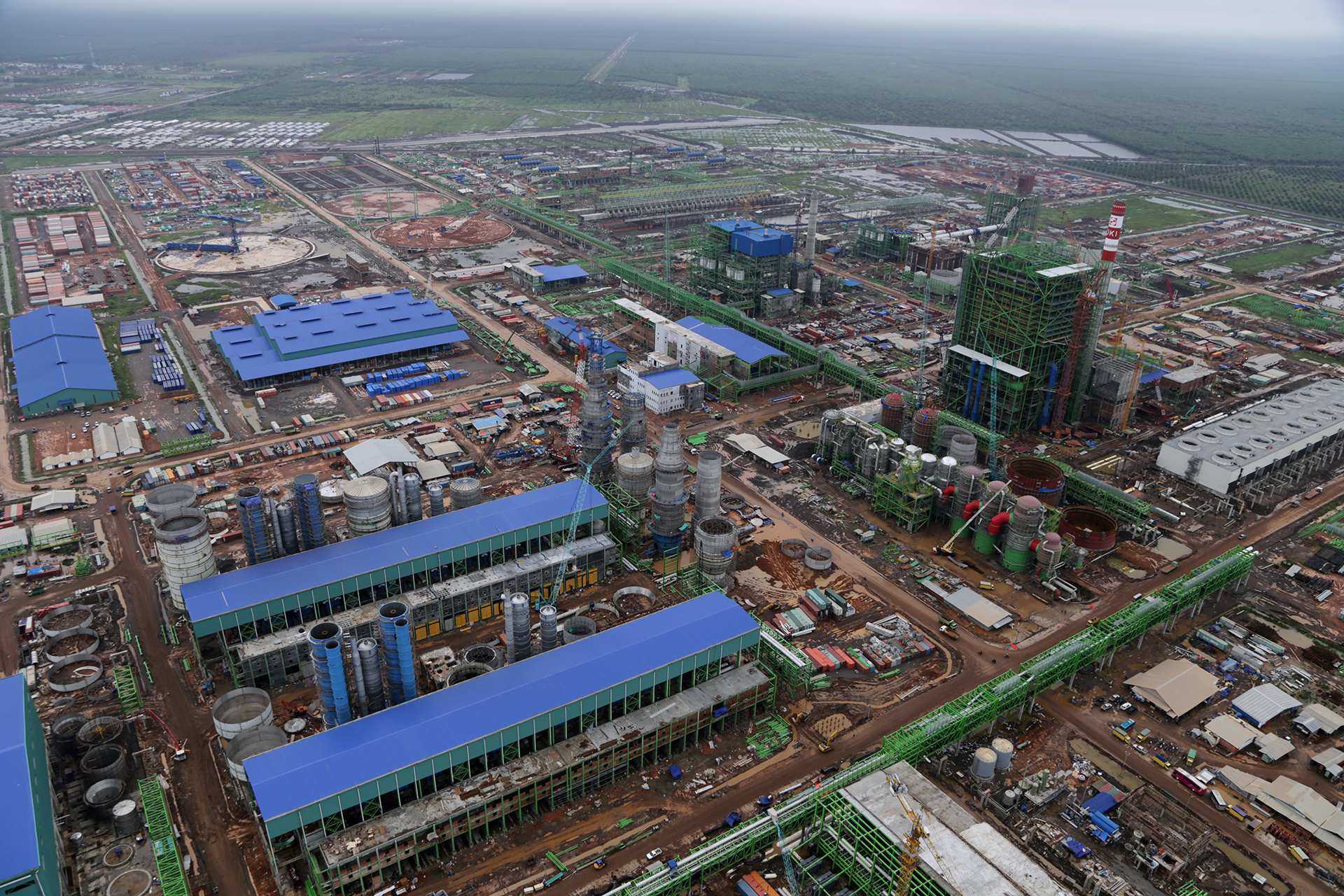
Now under construction in Ogan Komering Ilir (OKI) in South Sumatra, APP’s massive new pulp mill has a design capacity of 2.8 million ton/yr.
This look at APP’s new mill, due to open later this year in Ogan Komering Ilir (OKI), South Sumatra, is an excerpt from a feature appearing in the upcoming July/August issue of Paper360° and is offered here as a preview for Ahead of the Curve readers.
By AIDA GREENBURY
Representing an investment of about US$2.6 billion, the Asia Pulp and Paper (APP) mill now under construction in South Sumatra will be gigantic. This bleached hardwood kraft pulp mill is known in the industry because it will enable APP to significantly increase its production capacity, which is essential for the company to continue meeting growing market demands and further strengthen Indonesia’s contribution to global trade.
Questions have been raised about the fiber supply required by the mill and if it will jeopardize APP’s no deforestation commitment. APP feels these concerns are unmerited. In this article, we will provide a sneak preview into how APP will increase its production capacity responsibly to meet the needs of the mill. It will also provide a glimpse at the environmental technologies and standards to be installed and practiced.
Sourcing sustainability
First, it is important to underline that APP’s Forest Conservation Policy (FCP) commitment—which includes, among other things, no clearance of natural forest by its pulpwood suppliers since 2013—takes precedence over maximizing production. Furthermore, APP has initiatives underway that ensure it is able to increase its production capacity responsibly.
One key factor behind the decision to locate the mill in OKI is its position close to its fiber resource, which will minimize transportation costs. South Sumatra also offers an ideal position between the commercial centers of both Singapore and Jakarta. Longer term, APP plans to build a seaport in close proximity to the mill to allow easy access for transport and shipping goods out.
The mill has a design capacity of 2.8 million tons/yr, but will commence production at a low level and will gradually increase subject to demand and the availability of raw materials. A number of initiatives are already underway in the plantations that will supply OKI to optimize production for the mill, while maintaining the commitments made in the FCP.
To start with, APP is looking into increasing productivity and yield by improving control of pests and disease, reducing mortality and waste, and increasing efficiency in harvesting methods using mechanization techniques. Also, APP is researching alternative plant species that can provide better yields and thrive in wetter peatland conditions, and researching ways to reduce the risks of further forest degradation and fires through strengthened community forest initiatives in APP’s supply chain.
If these measures are still unable to produce the quantities of pulpwood needed for OKI to run at full capacity, supplies will be bolstered by woodchips from global suppliers that meet APP’s Responsible Fiber Procurement and Processing policy.
Technologies on-site
It has always been APP’s ambition to equip OKI with the most advanced environmental technology available today. The mill has been designed to achieve the highest industry standards on emissions and will meet the criteria of the European Union’s Integrated Pollution and Prevention Control (IPPC) Directive.
The mill will be powered by clean, self-sufficient energy generated from the pulp production process and wood bark gasification, which will reduce the need to use oil and gas in lime kilns by up to 80 percent. This technology also allows for more optimized use of bark and wood as a biofuel and, in addition to cost savings, will lead to significant reduction in carbon emissions.
Gasification is a technology for effectively converting biomass into a usable form of energy. The CFB (Circulating Fluidized Bed) gasification process works by partially combusting the biomass at high temperature using a controlled amount of oxygen and/or steam. The resulting product gas is a versatile energy carrier that APP will use in lime kilns to replace hydrocarbon-based fuels.
The mill will also use state-of-the-art technologies to treat effluent, including:
- centrifugal dewatering machines and belt presses to handle solid waste
- diffusion aeration systems
- concrete aeration tanks
- primary clarifiers to settle primary sludge
- secondary clarifiers to settle secondary sludge
- an emergency pond to handle deviations and maintain constant quality of effluent discharge; and
- cooling towers to maintain effluent temperature at below 35°C within the aeration tanks to ensure good bacteria growth.
In the future, those touring the woodyard will also be able to see seven drum debarker lines and two rotary debarker lines in action; a screening section with nine lines of gyrating screens; and chip crackers, wood savers and bark crushers all designed to optimize yield and wood recovery.
Investing in the community
However, what really excites APP most about OKI are not these advanced technologies, but the contribution we hope this mill will make to the South Sumatra community. The Governor of South Sumatra is committed to boosting job opportunities in the region and APP is committed to prioritizing South Sumatrans in the mill’s hiring policy. The mill will employ approximately 1,700 staff, and will create about 10,000 jobs in total both directly and indirectly.
The intention is for OKI to become a site with advanced environmental technologies and practices that APP can be proud of for years to come, and for the mill to become the center of a vibrant and thriving community in South Sumatra.
Aida Greenbury is the managing director/chief of sustainability at Asia Pulp & Paper.
For a modest investment of $174, receive more than US$ 1000 in benefits in return.
Visit www.tappi.org/join
for more details. |